Blog, Produits
créer un bec de saxophone: la matière première
The choice of material in the manufacture of a mouthpiece is certainly not trivial. This determines, together with the definition of the geometry and internal proportions, peculiarities and timbre of the mouthpiece.
There is no doubt, in our experience, that quality and choice of materials will have its weight on the characteristics of the final product.
I should emphasize that catalog and describe a sound is never simple and the subjective elements that come into play, a personal sensitivity shaped by their experiences in the field, by years of study and research entirely subjective that it was decided to deal with to get that personal sound that will distinguish our sound from the other and that we can define our « sound signature. »
This is why I find that the comparison tests are always the best: always evaluate something compared to something else, and then define a first starting point from which to start our research.
The CG Mouthpiece Italy mouthpieces are all made from solid bars of metal or hard rubber (the latter derived from the rubber plant – Caoutchouc).
Initially we used for our metal mouthpiece solid bars in both bronze and brass: each prototype was made in both materials as well as to evaluate each time the different peculiarities. The bronze chosen is a particular alloy in which the lead is absent, we selected for its excellent acoustic characteristics, physical and mechanical. It ‘also called « marine bronze » as mostly used in the shipping industry due to its resistance to corrosion and wear. And ‘undoubtedly the finest bronze on the market and that therefore a further added value to our mouthpieces. Our bronze has proved more difficult to machine than brass: the latter, especially in manual processing, is more « dry » and therefore easier to handle particularly for the benefit of processing times. But the bronze we selected has definitely more interesting acoustic features and, despite the greater difficulty in processing, we elected him as the only material from which « sculpt » our metal mouthpieces. Models of our production as the ROMA and FLORENCE, designed to give projection and brilliance to the sound, have particularly benefited from this choice: our bronze gave them a bright timbre and at the same time rich and full-bodied.
Most noticeable has proved the difference in acoustics in enonite and hard rubber mouthpieces.
Many of you will say « ebonite and hard rubber are not the same thing? ».
Often in the world of mouthpieces it is called « hard rubber » or « ebonite » any material other than metal. In many cases it is only plastic material derived from petroleum and therefore economic or otherwise of a composite material, mixtures of various resins and other.
The ebonite (word derived from ebony – wood) or rather the hard rubber is determined from the vulcanization process (thanks mr. Charles Goodyear!) of a mixture composed of resin rubber plant combined with sulfur and natural oils. It has excellent resistance to chemical agents, including acid and alkali as well as a very high resistance to humidity. This mixture, in the production of the bars, before undergoing the process of vulcanization is extruded at very high pressure and added to various diameters of pipes that will be in turn inserted into the autoclave for the curing process that will last a few days.
This process involves the use of pressure + heat (steam) which trigger a chemical reaction that combines the molecules of rubber with sulfur. Thanks to this reaction the elasticity and strength of the material is dramatically improved: the one that was soft rubber is now incredibly hard.
The Ebonite / hard rubber that we use is of the highest quality and there is provided in a range of diameters bars and often original and refined style with which we produce our limited series.
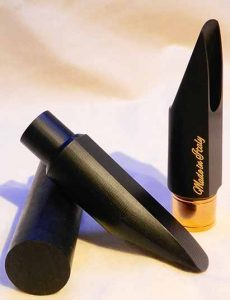
Hard Rubber sem-finished
These are already very stable but to be even more ensure that our mouthpieces retain their precise geometry, from the first stage of processing which generates semi-finished products until the precise craftsmanship of a « definitive » mouthpiece, we let spend not less than 4/5 months in which the semi-finished products can be further stabilized.
For our « no metal » mouthpieces we use two types of ebonite: hence the distinction we make in some models between Ebonite and Hard Rubber. The production procedure is always the one described above but what we call Hard Rubber has a higher content of rubber/caoutchouc, therefore the most noble part of the product.
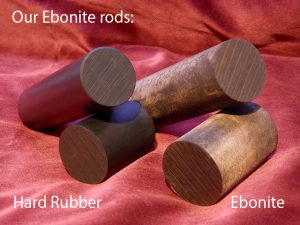
CG Mouthpiece ebonite & hard rubber rods
The latter material (Hard Rubber) is darker than at the sight, more dense and compact, working it is less dry than the ebonite « standard. »
In the photo below you can see the difference between the two materials: the Ebonite in the processing phase releases a yellowish powder (the raw material in fact contains sulfur) while the hard rubber more residues of black powder (I also assure you a sharper smell of rubber!).
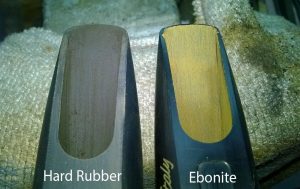
craftsmanship of a CG Mouthpiece
We can then consider the Hard rubber – in our distinction – a more noble material, definitely more expensive and more demanding manual processing.
There were many mouthpieces (all our prototypes identical model but different in the material) we have tested and that have made us discover the peculiarities of each of them:
- Ebonite more ready in the attack of the sound, there is a feeling that the material to vibrate more (feel of the contact of teeth / lips with the mouth). Sound slightly brighter than the hard rubber and easier to manage.
- Hard rubber: a more complex, robust, compact and harmonically rich timbre (see spectrum analysis). Maintains its tonal characteristics although strongly urged (f – ff – fff). Timbrically a little darker than ebonite.
In describing these differences I have considered not only the ear but also of the « input » of the body, of those sensations in perception that make me define a musician a « single vibrating body composed of instrument and instrumentalist ».. Those on which we should focus all of us when we practice the exercises of « long tones » and generally work on the sound.
The spectrum analysis will perhaps clarify the concept of « solid, compact and harmonically rich », again comparing the two analyzes (below the Ebonite, on top of the hard rubber). I have chosen to analyze the characteristic features of the main registers: low, central and high register on tenor sax:
Obviously this test aims to be comparative between the two materials under analysis, and closely related to the CG Mouthpiece Italy production and the materials we choose to create our mouthpieces. We not therefore claim to have absolute value.
I paid much attention to maintain the same distance from the microphone and the same position in the studio, as the same « intention » in playing.
The test setup was:
CG Mouthpiece Italy Syracuse model (ebonite & hard rubber – 8*) and Galileo brass ligature
François Louis reed
Tenor sax Rampone & Cazzani R1 Jazz solid bronze
AKG C214 mic
Focusrite Saffire Liquid 54 soundcard
recorded at: 96Khz/24bit
Leave a reply